Understanding MIG Welder Settings: Amps, Voltage, and Wire Speed
MIG welding is one of the most widely used welding processes in industries today due to its versatility and ease of use. However, to achieve clean, strong welds, it’s essential to understand the key settings on a MIG welder, specifically amps, voltage, and wire speed. In this guide, we’ll explore these essential settings for best MIG welder for beginners and provide tips to help you find the perfect balance for any project.
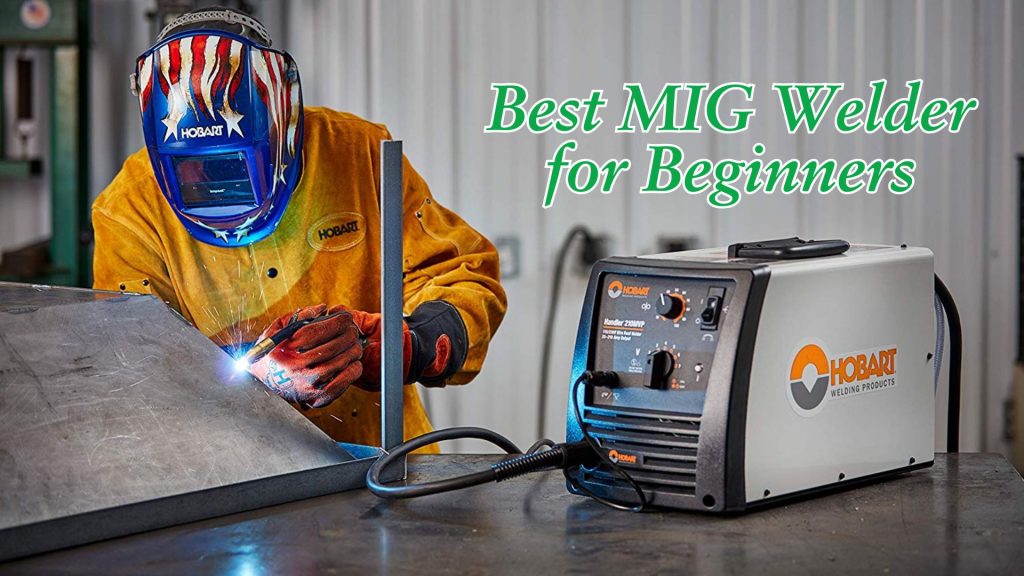
Why Proper MIG Welder Settings Matter
Setting up your MIG welder correctly is the foundation of high-quality welding. When your settings are off, issues like excessive spatter, weak penetration, and burn-through are likely to occur. Adjusting amps, voltage, and wire speed according to material thickness and type ensures better weld appearance, strength, and overall quality. Let’s dive into each setting to see how it affects the MIG welding process.
1. Amps in MIG Welding
What Are Amps? Amps, or amperage, is the amount of electrical current flowing through the welder. In MIG welding, amps control the heat and penetration of the weld.
How Amps Affect Welding: Higher amps produce more heat, which leads to deeper penetration in the material. Lower amps produce less heat, resulting in shallower welds. Adjusting amperage is crucial, as it helps you adapt to different materials and metal thicknesses.
Factors Affecting Amp Setting:
- Material Thickness: Thicker materials require higher amps for deeper penetration, while thin materials need lower amps to prevent burn-through.
- Wire Size: Larger diameter wires need more amps to maintain a stable arc.
Tips for Adjusting Amps: To achieve optimal amps, check the MIG welder’s user manual for recommended settings based on wire size and material thickness. Start within the recommended range and make minor adjustments as needed, depending on your project’s requirements.
2. Voltage in MIG Welding
What Is Voltage? Voltage in MIG welding controls the stability of the arc and influences the shape and width of the weld bead.
Role of Voltage in Welding: Voltage determines the arc length. A higher voltage produces a broader and flatter bead, while a lower voltage creates a narrower and more convex bead. Proper voltage setting leads to a smoother and more consistent arc.
Setting the Voltage:
- High Voltage: If the voltage is set too high, the arc may become too long and uncontrollable, causing excess spatter.
- Low Voltage: Insufficient voltage can cause poor fusion and a weak arc that’s prone to stalling.
Tips for Finding the Right Voltage: Observe the weld closely as you make small adjustments to the voltage. Most MIG welders come with a voltage range guide for specific materials; using this as a reference point can help you get started.
3. Wire Speed in MIG Welding
What Is Wire Speed? Wire speed refers to the rate at which the welding wire is fed through the gun. It directly impacts the amount of filler metal deposited and controls the heat input to the weld.
How Wire Speed Affects the Weld: The wire speed has to match the current setting to maintain a stable arc. If the wire speed is too fast, it can result in excessive heat and create more spatter. If it’s too slow, it can lead to burn-back, where the wire melts and fuses to the contact tip.
Setting the Wire Speed: To achieve optimal wire speed:
- Start with the manufacturer’s recommendations based on your selected amps and voltage.
- Adjust by listening to the sound of the arc. A steady “sizzling” sound indicates a well-balanced wire speed. If the arc pops or crackles, adjustments to wire speed or amps may be needed.
4. Coordinating Amps, Voltage, and Wire Speed
The best welds come from balancing all three settings: amps, voltage, and wire speed. A common approach is to begin with a middle-ground setting for amps based on material thickness, then adjust the voltage and wire speed until you achieve a smooth, consistent arc.
Examples of Basic Settings:
- Mild Steel: For 1/4-inch mild steel, start with around 200 amps, 22-24 volts, and a moderate wire speed.
- Stainless Steel: Stainless steel requires slightly higher voltage for clean penetration.
Use these guidelines to experiment and find the sweet spot for your setup.
5. Practical Tips for Beginners
Here are some additional tips to help beginners fine-tune their MIG welder settings:
- Use a Guide Chart: Many welders include a guide chart for amps, voltage, and wire speed. This is a great starting point.
- Watch and Listen: Sound is a powerful indicator of setting accuracy. The arc should have a consistent “sizzling” sound. Too much popping or hissing usually signals an adjustment need.
- Practice with Test Welds: Make test welds on scrap pieces to perfect your settings before starting your actual project.
Conclusion
Understanding and mastering MIG welder settings—amps, voltage, and wire speed—is key to achieving high-quality welds. By learning how each setting impacts the welding process, you’ll have better control over weld strength, appearance, and efficiency. Practice adjusting these settings based on material type, thickness, and your desired weld characteristics, and over time, you’ll gain confidence and precision in your MIG welding work.
With the right balance of amps, voltage, and wire speed, your welding skills will shine through in every project.
Leave a Reply